μ-MIM® Technical Newsletter Vol. 39 Quality Assurance Technology in μ-MIM
μ-MIM technology is not only a MIM production technology but also includes quality assurance technology for small complex metal parts. The reliable quality assurance technology development has been our guiding principle since our MIM business establishment – if there is no reliable evaluated data, no market will accept our parts.
It is commonly accepted that a few millimetre sized metal part evaluation is very difficult. We would like to explain the reasons of difficulties using examples in this issue.
Why the measurement technology development was required?
With the downsizing of devices with ever higher functionality requirements, the complete structure of metal parts has become very small to a few millimeter in length, having highly complex 3D structures. For example, high-precision metal parts with free design of curve, internal gear or complex side holes. In the MIM industry a near-net-shape sintered body production plus post machining methods is commonly deployed. However, in the case of small complex shaped parts requiring some 3D locational precision, the conventional MIM method often cannot satisfy the requirements in tolerance or mechanical properties.
On the other hand, our μ-MIM technology has been developed for net-shape production that aims minimum post-treatment for stable mass production of small precision parts. At the beginning of our MIM business in the 1990s, there were very limited method that can evaluate the metal parts non-destructively and we were not sure the measured data is reliable; especially in the complex structures like free-curve, internal or helical gears.
Changes of measurement technology
At the same time, 3D-CAD drawing was commonly deployed and 3D measurement demand increased. In 3D measurement, the tactile measurement is commonly applied, however, our μ-MIM parts are too small to measure even with the smallest available prove. Thus, we decided to develop the non-contacting measurement system.
Generally, electron beam or X-ray is deployed for metal parts evaluation in non-contacting measurement since the visible light does not penetrate the metal parts, nor a serious reflection. For example, scanning electron microscopy is capable to observe the distances precisely, however, it is not beneficial to measure whole 3D or internal structure non-destructively. The X-ray CT scanner does observe 3D or internal structure non-destructively. Nevertheless, for μ-MIM parts observation, the measurement spot of a few μm is required, thus available equipment was very limited. Fortunately, we come across the optical measurement system that deploys the breakthrough technology and over 20 years we have cutivated the measurement experiences and knowledge.
μ-MIM technology beyond 2022
Now that we have accumulated small metal parts evaluation knowhow, we can provide confident quality assurance data in 3D complex part also, thank to the great development of data processing technology. Also, a high resolution analysis plus numerical simulation reveals the actual quality difference from conventional MIM to our μ-MIM that realises your ideal metal part serial production.
The further details are presented in our webinar which will be held on 19 Oct, Wednesday. If you are interested in, please register from our webpage (Micro-MIM Webinar | Make your manufacturing technology with our micro-MIM)
Exhibition
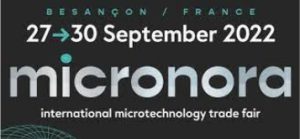
We will exhibit at the Micronora trade fair in Besançon, France with Incus GmbH between 27-30th September. We would be delighted to welcome you to our stand to see and touch our actual μ-MIM parts. Our booth is C504.
Column
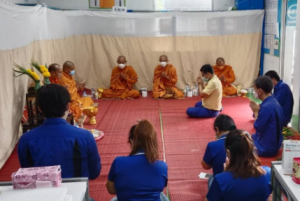
TAISEI KOGYO (THAILAND) CO., LTD. celebrated its 10th anniversary. “Tham bun” was held in August as part of the 10th anniversary events. “Tham bun” is a Buddhist ceremony to accumulate good karma. The idea is that by doing “Tham bun”, the good karma will come back to you in the future. We had the monks chanting a sutra. We prayed for thriving business and for the health and well-being of our employees. After the monks left, everyone enjoyed delicious food together. We appreciate your continued support of Taisei Group.
Conclusion
Cracking, slumping or blistering is commonly observed due to the binder swelling and/or residual stress difference between the surface and interior. It is possible to avoid these problems by selecting appropriate organic solvents and temperature control.
The catalytic deboning uses sublimation of binder, thus it is possible to decompose the binder in relatively short processing time with minimizing the deformation. However, with a strong acidic atmosphere, theapplicable metal material option is limited.
In the sintering process, the necking, which is bridging the metal powders by thermal diffusion, starts at the sintering temperature. Once the necking starts, the shrinking is observed and increases the density, thus before starting the necking reaction, all the organic components should be decomposed and gas between the powders should be removed. In the sintering process, the unwanted chemical reaction, such as oxidation or carbonization, leads to mechanical property loss, therefore a precise atmosphere control with low heating rate at the beginning of the process is required. Also, when it reaches the sintering temperature, some add it vegetal can be evaporated.