What is μ-MIM®?
The 4 best reasons to manufacture high-precision components with μ-MIM®
High tolerance
With over 25 years of our original μ-MIM technology development, we have achieved unprecedented tolerance satisfaction in an as-sintered state. In conventional MIM, the tightest tolerance is +/- 30 μm, while μ-MIM® achieves +/- 10 μm.
Compared with the latest machining technology, the tolerances achieved are lower, but still competitive with conventional machining. Plus, μ-MIM® technology is a net-shape production technology that uses minimal post-processing to reduce the risk of tolerance deviations in 3D locations. Productivity and preciseness are μ-MIM® technology's unique strengths, which help realise your ideal metal part production to the market.
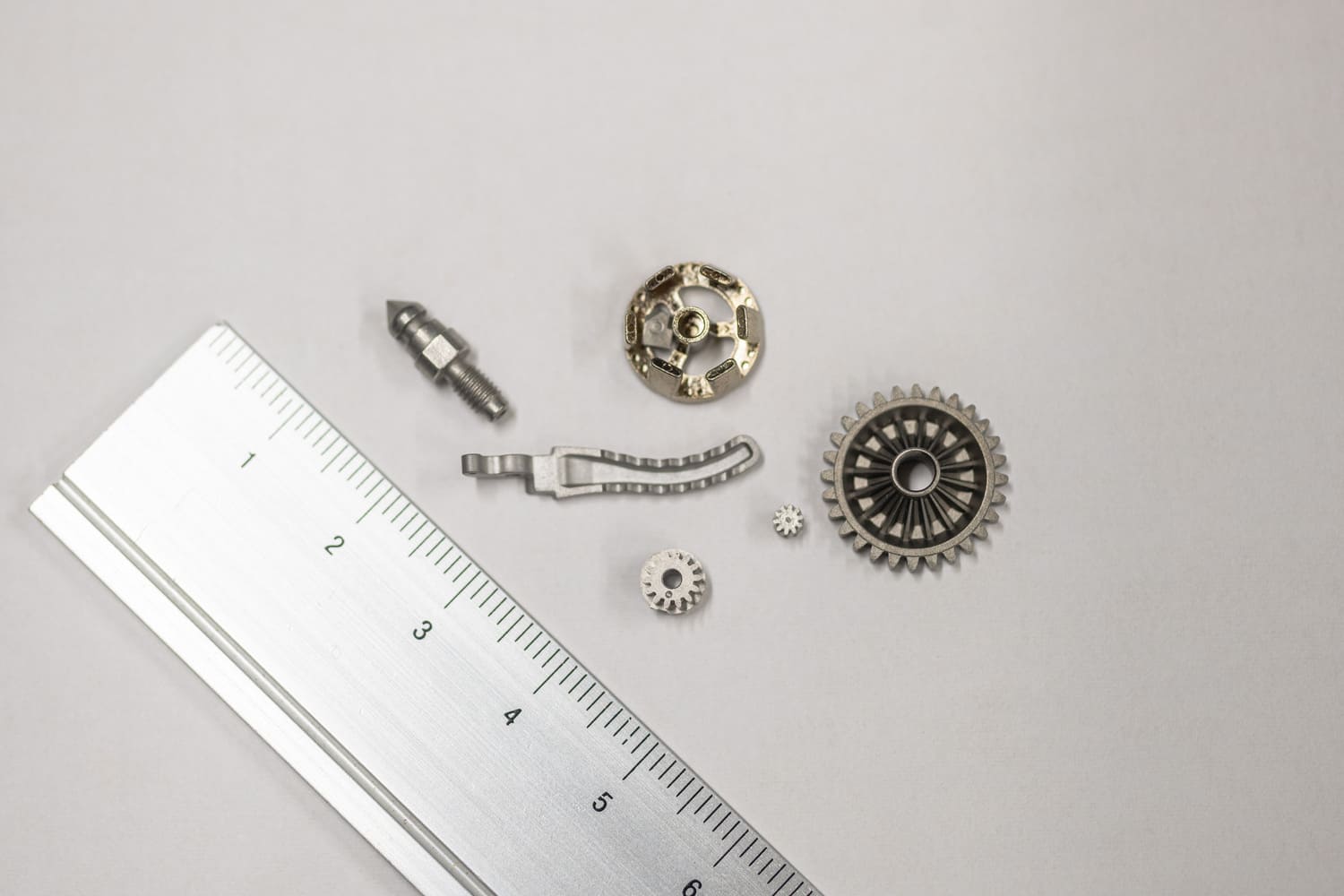
Material varieties
This is due to our original feedstock processing, which we developed based on our knowledge and experience in plastic injection moulding history. We make binder by ourselves.
Since our lead time for feedstock development could be relatively short, newly developed alloy powder can also be used for production, provided the right size and shape of powder is available for procurement.
We are capable to optimise the feedstock for each product's stable production, and newly developed alloy powder can also be used for production.
Please contact us even if the material is not on the list.
Design freedom
μ-MIM® technology was developed with a focus on serial production of small complex designs, thus with a minimum of additional machining production has been realised.
Because μ-MIM® technology was developed with a focus on serial production of small complex designs, we are able to produce small features or impossible to demold designs with a minimum of additional machining.
Additionally, our 3D-μMIM® technology achieves even a high level of design freedom that you have not expected from traditional MIM.
Our μ-MIM® and 3D-μMIM® technology realise your difficult-to-machined design serial production.
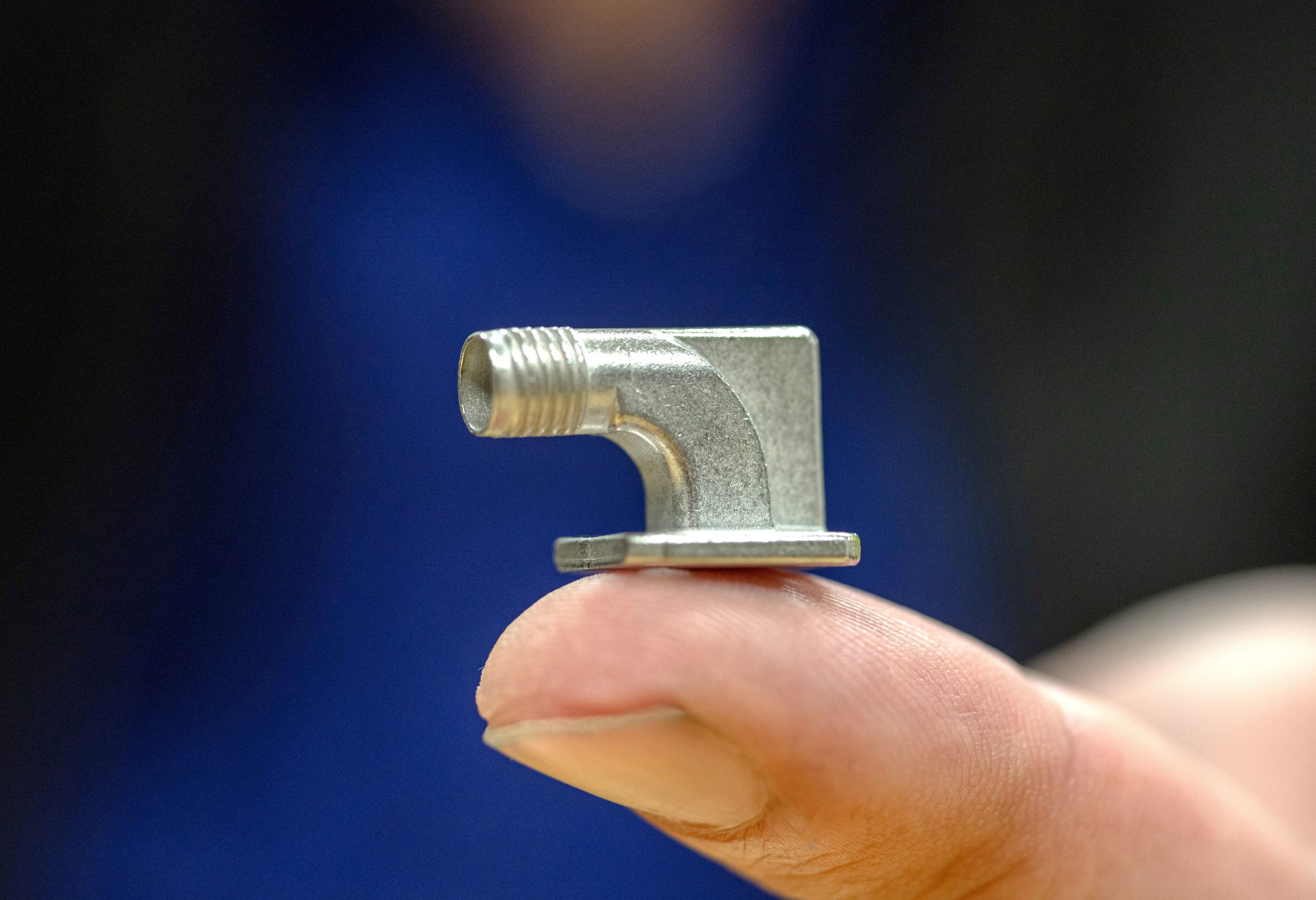
Stable mass production
We know that the production of small, complex metal parts requires even better process control than conventional MIM, because the quality of the preceding step has an even greater influence on the parameters of the following step.
The production of small, complex metal parts requires good uniformity in a feedstock pellet since the product size can be smaller than a pellet size.
We have precisely controlled our production process from feedstock to sintering, plus the final dimensional measurement process under the certified ISO 13485 quality assurance system.
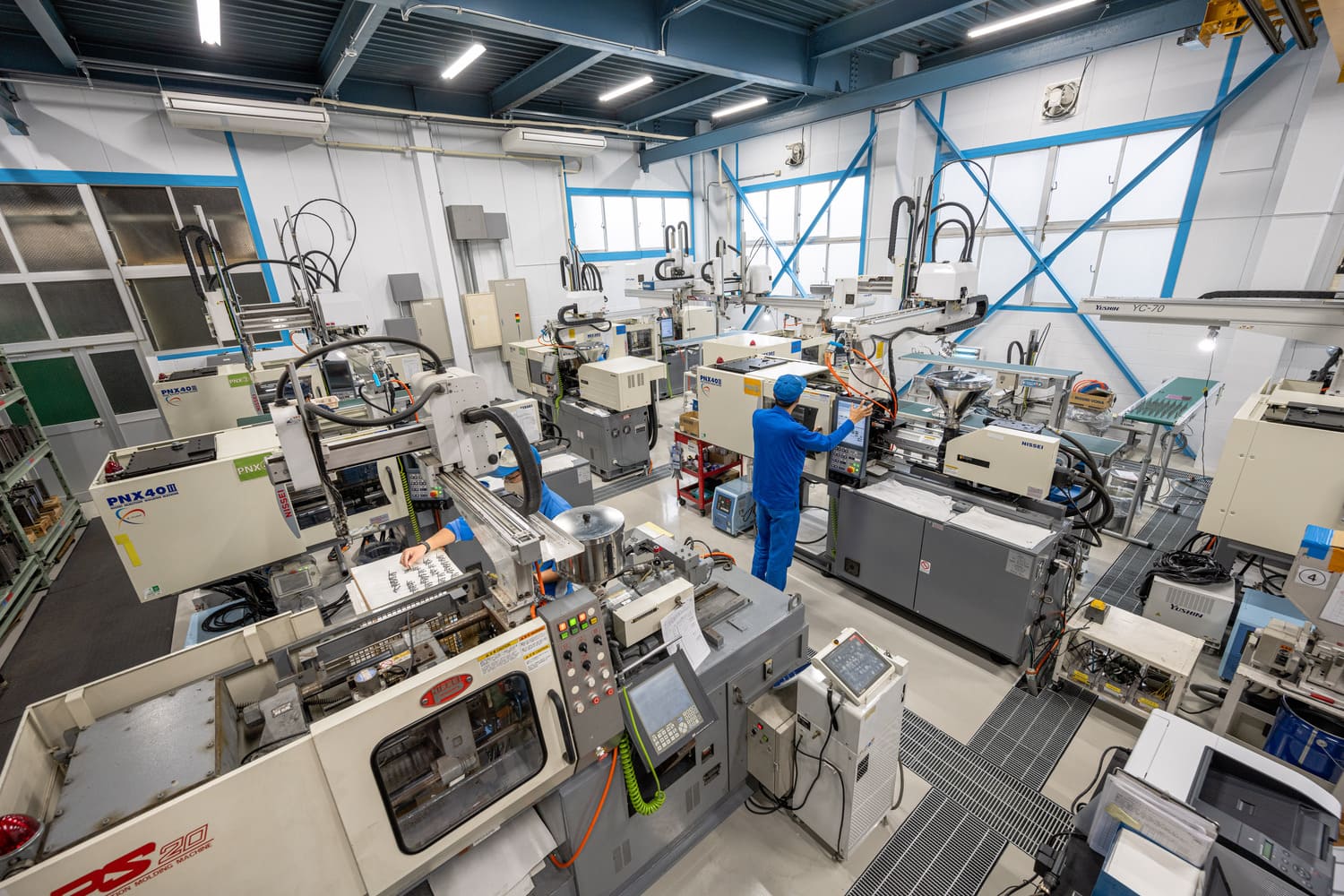
What we can offer our clients
Outstanding expertise
Broadest range of materials
Tiny components
Design freedom
Stable serial production
High quality
Parts smaller than a grain of rice
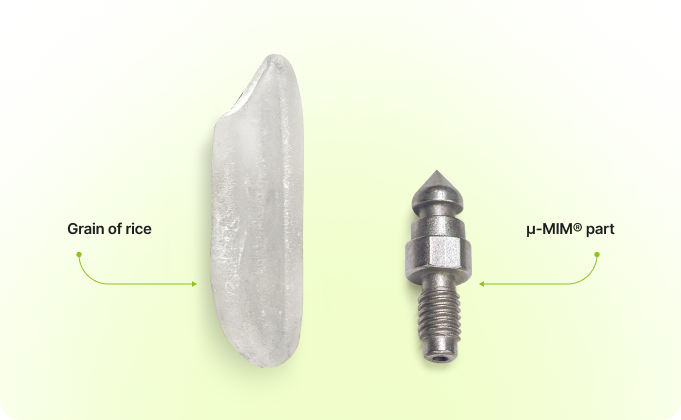
High accuracy, density, strength and surface quality
High accuracy
High density
High strength
High surface quality
Materials
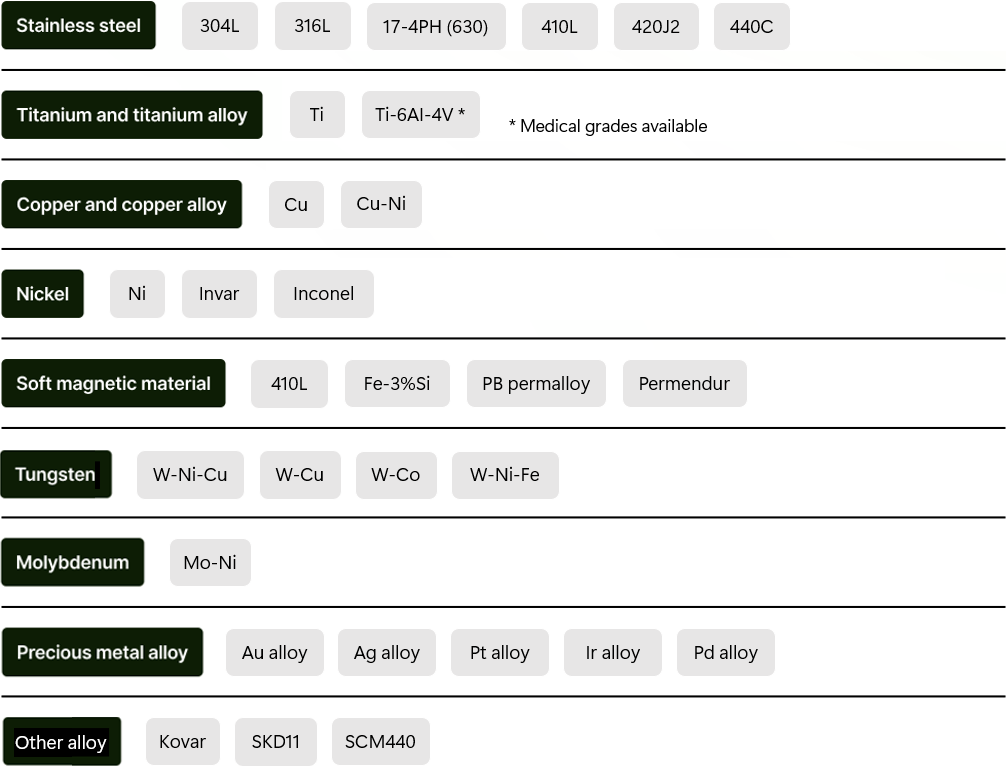
3D-μMIM® Technology
3D-µMIM® is our unique lost-core process that enables the mass production of components with complex geometries with hollow structures and undercuts that are difficult to fabricate using conventional MIM or machining.
First, a sacrificial plastic mould (SP mould) is produced in a mould and inserted into another mould; the SP mould is completely disassembled during debinding and sintering, and a 100% metal component is manufactured in the end.
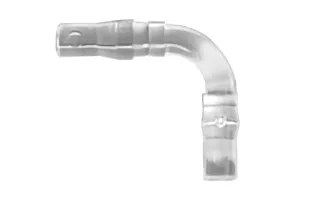
Sacrificial plastic mould
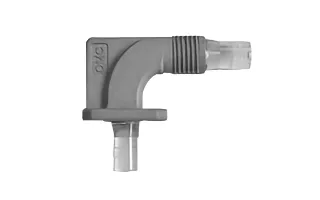
Metal feedstock injection
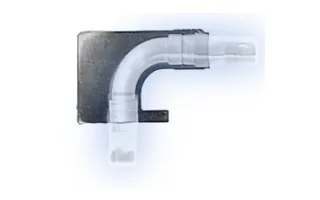
Degreasing and sintering
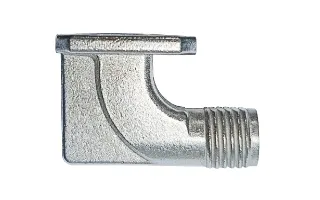
Sintered component
Free-form component examples with 3D-μMIM®
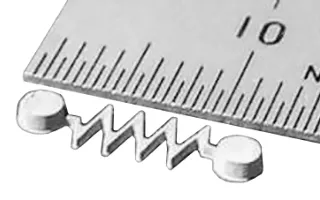
Zigzag spring
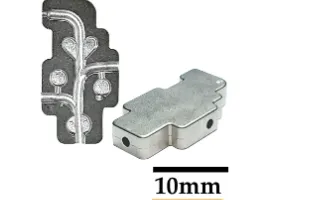
Inner curved flow
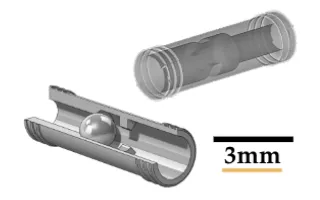
Hollow structure
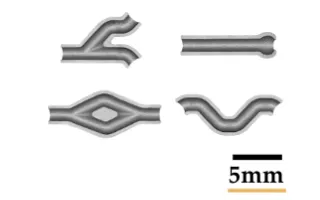
Micro pipe
LMM 3D Printing Xμ-MIM® technology
µ-MIM® evaluation & measurement technology and quality assurance
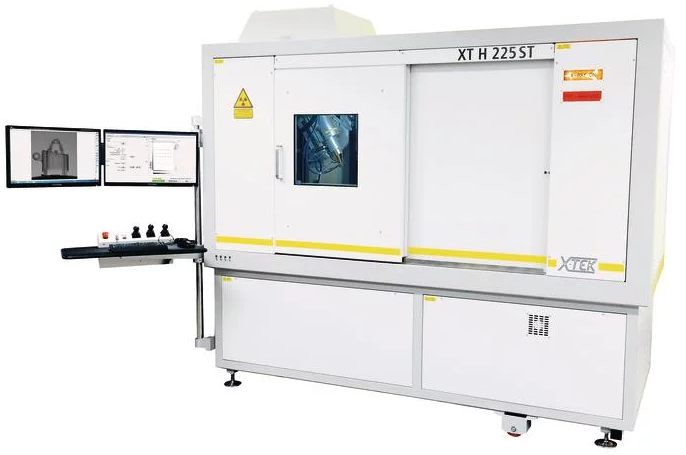
X-ray CT
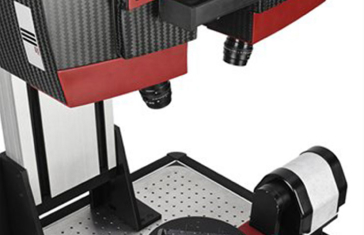
Optical 3D measuring system
Differences between MIM and μ-MIM®
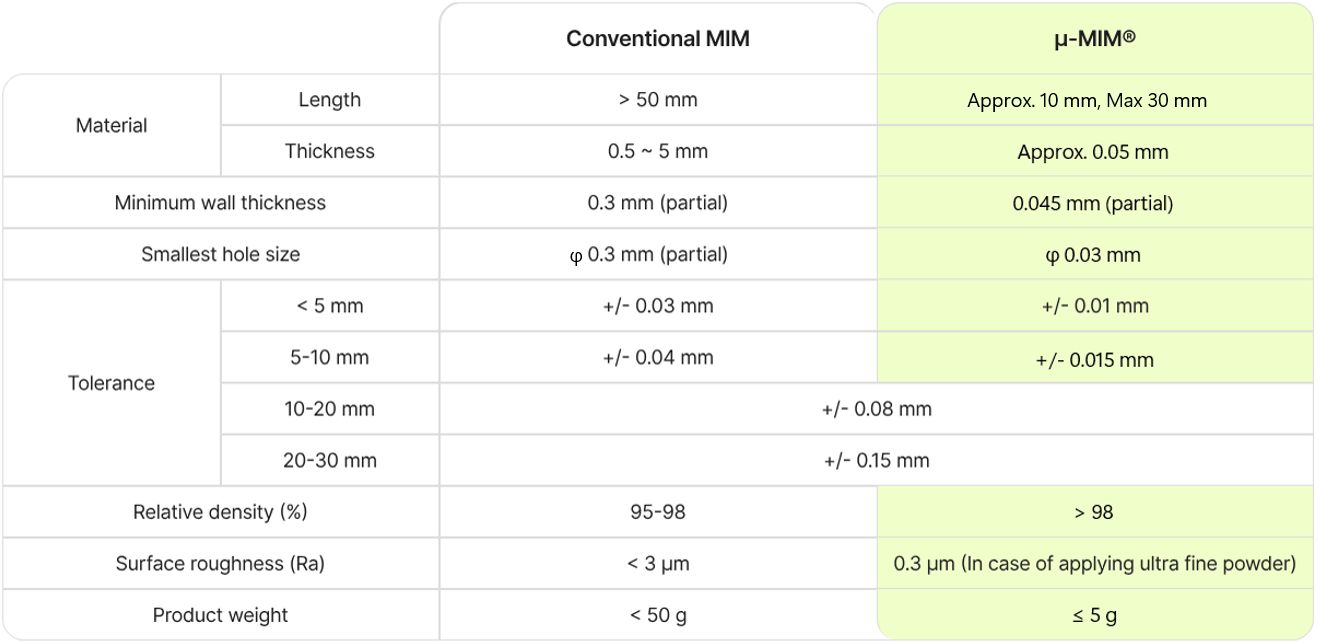
Comparison with other manufacturing methods
How we help you solve your technology challenges
Case 01
The challenge
Because the shape of the component was too complex to make at once, multiple parts were made separately and then had to be assembled into a single part.
The solution
We can produce parts in a net shape using a die in an integrated mould, which helps to reduce costs and shorten delivery time, and also leads to downsizing.
Case 02
The challenge
Because the material had a complex shape and was difficult to process, companies refused to produce it.
The solution
We are able to produce components with complex shapes and materials that are difficult to machine, this way we can make a valuable contribution to the development of completely new products
Case 03
The challenge
Burrs, etc. were produced, post-processing was necessary, and the yield rate was low.
The solution
The realisation of net-shape has made post-processing unnecessary and enabled highly accurate production.
Case 04
The challenge
Machine processing reached its limits in mass production, so that the component could not be produced in the desired quantity.
The solution
We offer manufacturing in dimensions that cannot be achieved by machining, both in terms of quantity and shape, resulting in lower costs and shorter delivery times
Why other companies like to work with us
Download our company flyer about our µ-MIM® technology
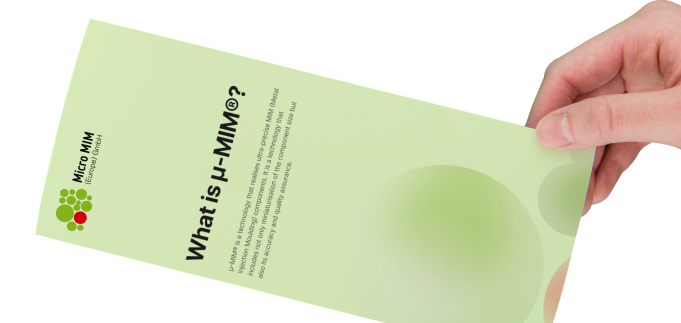
Schedule an initial consultation with one of our experts today
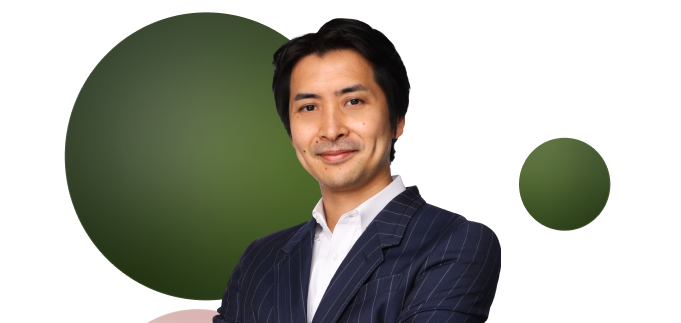