μ-MIM® Technical Newsletter Vol. 25: New year greetings
Thank you for subscribing our technical newsletter. We would like to tell the new year greetings from our company president and staff.
President
We would like to show exponential development in this year in terms of agility.
We understand that our customers were not satisfied with our trial sample delivery time. In metal injection moulding production it is crucial the mould tooling since the injection moulding process is the only process that we can control the components morphology, however, mould tooling is the most time-consuming process in metal injection moulding production. We have implemented some technical developments such as mould 3D high-resolution scanning with CAD data analysis or injection moulding simulation analysis to minimise the optimised mould production. However, these developments were limited to reduce the mould tooling time and importantly, it was not able to eliminate the tooling cost in the trial stage. Though, our trial mould can apply for the serial production, in case of the design of the final component is not confirmed in the trial stage, the mould investment is hugely affecting our customer’s decision. Therefore, we will install some metal powder additive manufacturing (metal AM) system into our production.
We have been investigating metal AM machines over the past few years, and finally, we have found some metal AM machine that satisfied our requirement that can perform equivalent to our micro metal injection moulding (μ-MIM®️) technology manufacturing. Further information regarding this AM manufacturing system in our company will be announced in the 1st quarter period of 2021. Further agility improvement in our present serial production line, we have been installing digital sensing and control systems. We will step forward to realise the higher level of manufacturing and quality control.
We established our metal injection moulding or MIM manufacturing business 27 years ago. At that time, MIM technology was new and there were many spaces to develop. Now MIM is also considered one of the well-developed manufacturing methods, yet the popularity is still lower than other metal processing method, such as machining and stamping. However, metal AM boom is greatly supporting the not only the powder metallurgy recognition but also the surrounding technology development and cost reductions, for example, the powder manufacturing, laser system, AM machine and so on. We will keep developing our manufacturing technology utilise these advantages to realise our customers’ ideal components.
I wish you will have a very happy new year and great development in your business. We are looking forward to receiving your requests.
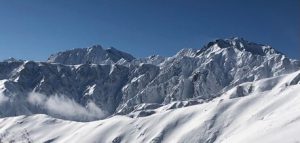
Staff
Thank you very much for giving us the opportunities to work with you in the past years and we wish you all to have a very happy new year. There were very limited opportunities to see our customers face to face in 2020. However, it was a great opportunity to enhance our web service quality improvement or in-house digital production control systems. In this year, we are going to organise some webinars to introduce our μ-MIM®️ technology progress and trends in the powder metallurgy industry. We wish we will be able to have stronger relationships with you and we are looking forward to discussing your any metal components ideas.
Conclusion
Cracking, slumping or blistering is commonly observed due to the binder swelling and/or residual stress difference between the surface and interior. It is possible to avoid these problems by selecting appropriate organic solvents and temperature control.
The catalytic deboning uses sublimation of binder, thus it is possible to decompose the binder in relatively short processing time with minimizing the deformation. However, with a strong acidic atmosphere, theapplicable metal material option is limited.
In the sintering process, the necking, which is bridging the metal powders by thermal diffusion, starts at the sintering temperature. Once the necking starts, the shrinking is observed and increases the density, thus before starting the necking reaction, all the organic components should be decomposed and gas between the powders should be removed. In the sintering process, the unwanted chemical reaction, such as oxidation or carbonization, leads to mechanical property loss, therefore a precise atmosphere control with low heating rate at the beginning of the process is required. Also, when it reaches the sintering temperature, some add it vegetal can be evaporated.