μ-MIM® realises quality micro gears!
In the previous issue, we explained that gears with diameters of a few millimetres, small modules in special shapes such as bevel and bevel teeth (bevel, miter, helical and etc.) are difficult to machine, and are typical of high cost gears. μ-MIM® technology has experienced various types of those micro special gears serial production and in this issue, we would reveal the backstage of the quality micro gear serial production.
High precision processing by μ-MIM®
- Dimensional accuracy ±0.1% is achieved
What causes such gear to be highly difficult and expensive? It is not only an issue of long processing time, but also the limitation of tool itself. The tools of micro-machining are made of difficult-to-machine steel and the tools requires a longer lead time, since the tool itself as difficult-to-machine materials are also machined in not in the quick serial production lot but in a small custom designed lot. Generally, the limitation of gear machining is around module 0.15 mm and the small gears below this requires even special custom-made tools, and this is reflected in the cost. Unfortunately, those expensive tool life is not that long since the tool itself size is very small too for micro gear processing.
Another difficult point for micro gear machining must deal with the chips. In the case of broaching, the tool diameter of less than 10 mm, required special custom-made. However, smaller the diameter, more likely to damage the tool due to the chip discharging. Even the broaching, the through hole processing becomes difficult in smaller size, thus, no wonder that the machining the non-through hole in small size chip problem For broaching tool longer the processing length gives better surface and tolerance in certain size. However in the case of small gears, the long broaching tool length becomes the worse the quality since the tool itself strength and tool holding are not satisfied. Therefore, it is difficult to mass-produce micro gears with high design freedom, high precision acquiring using high hardness material.
Our μ-MIM® technology might solve these problems. Our original binder system realises high flowability and precise moulding. Thus, a complex small designed gear is serial produced. Also, our highly skilled mould partners provide net-shape gear mould cavities for stable quality serial production. We have experienced various types of gears, such as gear with full circumferential tooth cutting for sure, partial tooth flanks gear, special tooth geometry, two-stage gear and many more. Please refer another issue for more information on this area of technology and materials.
Integrated shafts and gears reduce the number of components
One of the best features of MIM is complex design serial production so parts’ integration are capable and recommended. For example, set screws, keys, pins, splines etc. are used to fix gears together or shafts, but MIM enables to integrate components as a unit maintaining high precision and strength. Therefore, we can offer proposals of space-saving and cost-saving by reviewing the design in all drive units, where the demand for micronising is increasing.
In addition, 3D locational tolerance is more important for micronising and functionising the metal component. From this point of view, our μ-MIM® technology realises the net-shape stable quality production, thus we can push your dream gear into market in shortest possible time.
Hello to the world
This is Anshul Chhabra, working as a business development manager - North America at Micro MIM Japan Holdings Inc. I joined our Neyagawa, Osaka office in April 2023 and I am still getting familiar with our Micro MIM technology. I have been working in Japan for about 7 plus years now and have been involved in various business development roles across Asia and North America. I always thrive to be a problem solver and like to work together with the client to come up with the best solution.
Since this is my first time moving to Osaka, I spend my weekends mostly exploring the Kansai area. I also enjoy playing golf, hiking and long drives.
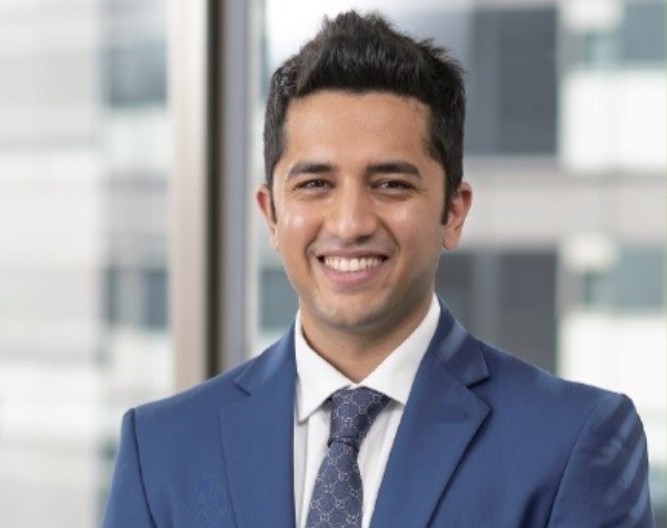
Download the PDF file
Conclusion
Cracking, slumping or blistering is commonly observed due to the binder swelling and/or residual stress difference between the surface and interior. It is possible to avoid these problems by selecting appropriate organic solvents and temperature control.
The catalytic deboning uses sublimation of binder, thus it is possible to decompose the binder in relatively short processing time with minimizing the deformation. However, with a strong acidic atmosphere, theapplicable metal material option is limited.
In the sintering process, the necking, which is bridging the metal powders by thermal diffusion, starts at the sintering temperature. Once the necking starts, the shrinking is observed and increases the density, thus before starting the necking reaction, all the organic components should be decomposed and gas between the powders should be removed. In the sintering process, the unwanted chemical reaction, such as oxidation or carbonization, leads to mechanical property loss, therefore a precise atmosphere control with low heating rate at the beginning of the process is required. Also, when it reaches the sintering temperature, some add it vegetal can be evaporated.