μ-MIM® Technical Newsletter Vol. 19: Evolution of additive manufacturing Vol. 1 (Metal AM outline)
The additive manufacturing (AM) technology has been actively developed in Japan since AM was promoted as a national project in 2016. We would like to introduce the AM trends from the perspective of metal injection moulding or MIM manufacturers.
Classification by powder supply and printing method
Supplying metal powder used in the metal 3D printer is roughly divided into 2 methods. One is supplying to the on-site printing part by a nozzle and the other one is spreading the powder over the existing layer by a roller in advance. The on-site nozzle supply type has higher material yield than stacking layer by roller type because the supplied powder is consumed almost 100%. However, it is required to compose enough quantities of columns to support the product structure during the process, thus, the total material yield becomes low in many cases. The stacking layer by roller method, it is required to spread equally on the whole processing area, thus, the material yield is low. However, the unused powder act as supporting columns during the process, therefore, it is possible to reduce the post-processing steps after printing. Additionally, a high percentage of unused powder is reused nowadays. The printing method can be sorted into selective sintering (SS) and binder jetting. While the metal powder is the sintered during printing by SS, binder jetting requires debinding and sintering like metal injection moulding or MIM after printing. In binder jetting, the adhesive is printed on a required area to bond the metal powder to form a product structure. The heat source in SS has been studied intensively and the printing speed increased drastically in the last few years. In 2016, it is launched 50 cm³/hour printing machine and it is targeted to achieve 250 cm³/hour or even 1000 cm³/hour as the next-generation machine. The binder jetting printing speed is higher than the SS. The printing speed of 60-100 cm³/hour machine has already been in the market.
Metal powder used in metal AM
In the metal AM, the spherical powder is employed as well as metal injection moulding or MIM. There is a very limited problem in metal injection moulding or MIM manufacturing if the fine metal powders are mixed. However, in metal AM, the too-small particle leads to deterioration in printing quality. Therefore, both upper and lower size limit tends to be set for metal AM. Besides, since the reduction reaction during the SS sintering process cannot be expected, the metal powder produced by expensive gas atomization is applied most. Due to these limitations, the AM powder is even more expensive than metal injection moulding or MIM powder, which is the most expensive in the conventional powder metallurgy.
Hurdle of “30µm”
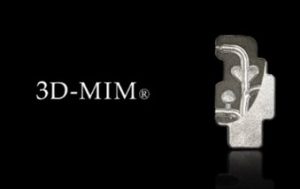
A metal 3D printer contains various latest technologies, such as employing powder with strictly limited particle size, multiple heat sources, and adopting a highly accurate system to control moving parts. The development of metal 3D printers in the last few years is remarkable, and it must have brought great benefits to other industries. However, there seems to be still a high hurdle for dimension control of ≤ 30 µm. The 3D printer has gained productivity to compete with other metal processing methods, though it is necessary to wait for a further breakthrough to achieve ≤ 30 µm tolerance requirements. Our manufacturing division, Taisei Kogyo Co., Ltd., has µ-MIM® (Micro MIM) and 3D-MIM® that mass-produce complex shapes with an accuracy of ± 10 µm if a part is ≤ 5 mm. We continually contribute to the development of metal 3D printer technology with the debinding and sintering Know-How that we have cultivated through metal injection moulding or MIM manufacturing.
Column
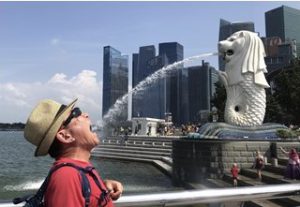
I am Hikoji Okuyama, in charge of Research & Development in Japan. I have joined the company in March 2019 so I am relatively new. Although I am not young anymore, I find every day something new in the metal world, which requires deep knowledge. I believe this will keep my brain sharp! On the weekends, I play tennis and go cycling. In winter, I also enjoy skiing. Another thing I enjoy is travelling – I went to the Scandinavian and Baltic countries with my son last year in the wintertime. That was really cold!
Conclusion
Cracking, slumping or blistering is commonly observed due to the binder swelling and/or residual stress difference between the surface and interior. It is possible to avoid these problems by selecting appropriate organic solvents and temperature control.
The catalytic deboning uses sublimation of binder, thus it is possible to decompose the binder in relatively short processing time with minimizing the deformation. However, with a strong acidic atmosphere, theapplicable metal material option is limited.
In the sintering process, the necking, which is bridging the metal powders by thermal diffusion, starts at the sintering temperature. Once the necking starts, the shrinking is observed and increases the density, thus before starting the necking reaction, all the organic components should be decomposed and gas between the powders should be removed. In the sintering process, the unwanted chemical reaction, such as oxidation or carbonization, leads to mechanical property loss, therefore a precise atmosphere control with low heating rate at the beginning of the process is required. Also, when it reaches the sintering temperature, some add it vegetal can be evaporated.