μ-MIM® Technical Newsletter Vol. 31: Debinding process in MIM
The debinding or degreasing process is unique in powder metallurgy among metal processing. In the compaction powder metallurgy method, a few percent of the binder is contained in total volume. Thus the debinding process is included in the temperature increment part of the sintering process. On the other hand, MIM feedstock contains 40% or more in volume ratio, thus, the degreasing process is clearly separated from the sintering process and carefully controlled. This time, we will introduce the debinding process.
Variety of debinding process
The debinding process can be separated into 3 types according to the degreasing reaction, such as thermal, solvent and catalytic. The easiest method is thermal debinding. The thermal debinding uses diffusion, osmosis reaction to decompose the debinding. The solvent debinding can be divided into 2 types of state such as vapour and liquid immersion. In the solvent debinding, the organic solvent is commonly applied and water, supercritical fluid, e.g. carbon dioxide are also applied. In case of using the water as the debinding solvent, it is required to use the water-soluble or water-reactive polymer. The catalytic debinding uses strong oxidative vapour, such as nitric acid, thus it is limited to the applicable metal material. However, the debinding temperature is lower and the processing time is shorter than the thermal debinding. Therefore, it is possible to minimise the deformation.
Requirements in the debinding process
In any type of debinding process in MIM, it is required to decompose the binder as much as possible in a short processing time without any unwanted deformation. The binder is commonly composed by mixing a few types of polymer, e.g. decompose lower and higher temperature polymer. The decomposition must process without deformation, thus the debinded reactant gas evaporated from the surface gradually. The slow decomposition leads to lower risk of deformation, however, too slow decomposition will decrease productivity dramatically and in some cases, unwanted side reactions occur and they lead deformation. Additionally, it is impossible to eliminate 100% of the binder after the debinding process or when we put the component into the sintering furnace, otherwise the component shape is lost.
Debinding process of μ-MIM®
Most MIM manufacturers deploy debinding furnaces separately from the sintering furnace in their production line, while we use the one-step furnace. From the productivity point of view, the debinding process takes a much longer time than the sintering time, thus introducing debinding furnaces is worth it. However, the debinded brown part is extremely brittle, therefore extra careful handling is required. From this point of view, we have deployed one-step furnaces to our production since we established the MIM production line. The brown part handling is a large risk to us since we do small complicated designed metal parts only. As mentioned before, it is impossible to eliminate binder contamination in the sintering furnace, therefore the furnace atmosphere control is important for quality control. We apply the specially designed furnaces for μ-MIM® production that were developed with the furnace manufacturer.
Reference:R.M. German, A Bose, Injection moulding of Metals and Ceramics, ISBN; 978-1878954619, 1997
Column
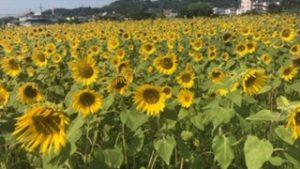
Hello everyone. This is Noriko Okamura from the Tokyo office. This summer, I was looking forward to watching the soccer games at the Olympics in the stadium. However, it was not realised, which was a pity! Normally the host city of the Olympic games is very busy with all the tourists and people related to the games. This time, the Tokyo Olympics was held in the vicinity of stadiums and other areas where games were held and we who live in the Tokyo metropolitan area also had to enjoy it through the TV. There were many moments that were so moving by the athletes! The photo shows the sunflower field near my place. I like the way it blooms as well as the language of the flower, which is “adoration” or “I only see you”. Although we had a lockdown in the Tokyo metropolitan area, the summer became a little brighter due to the Tokyo Olympics and the sunflowers.
Conclusion
Cracking, slumping or blistering is commonly observed due to the binder swelling and/or residual stress difference between the surface and interior. It is possible to avoid these problems by selecting appropriate organic solvents and temperature control.
The catalytic deboning uses sublimation of binder, thus it is possible to decompose the binder in relatively short processing time with minimizing the deformation. However, with a strong acidic atmosphere, theapplicable metal material option is limited.
In the sintering process, the necking, which is bridging the metal powders by thermal diffusion, starts at the sintering temperature. Once the necking starts, the shrinking is observed and increases the density, thus before starting the necking reaction, all the organic components should be decomposed and gas between the powders should be removed. In the sintering process, the unwanted chemical reaction, such as oxidation or carbonization, leads to mechanical property loss, therefore a precise atmosphere control with low heating rate at the beginning of the process is required. Also, when it reaches the sintering temperature, some add it vegetal can be evaporated.