Comparisons and characteristics of compaction, MIM and HIP in terms of density
Metal components manufactured by powder metallurgy tend to be regarded as having a low density compared to machined or stamped wrought material. Although, low density can be an advantage depending on the applications, but in general operations, high density is required to meet the mechanical strength requirements assumed in the design phase. In this issue, we introduce the characteristics of powder metallurgy from the perspective of density.
Comparison among powder metallurgy methods
The density of sintered components manufactured by metal injection moulding (MIM) or powder compaction moulding (CM) has a few percent of voids in relation to the theoretical density. When stainless steel powder is deployed, sintered components with densities of around 92% by compaction and over 98% by MIM are obtained. If a density of over 98% is obtained, voids do not have a great impact on the tensile test strength. However, if even a few percent of voids are not allowed, hot isostatic pressing (HIP) is deployed as post processing.
Characteristics of compaction, MIM and HIP
CM is the most productive method in powder metallurgy. As the powder is compacted with only a few percent by volume of the binder, thus the debinding process is shorter than MIM. In CM, the powder is compressed and deformed thus, the oxide film layer on the metal powder surface is destroyed. As the result, the fresh metal surfaces are contacting, therefore a relatively short sintering time is required. Although, there are many restrictions in CM design, it is possible to control dimensional accuracy at a high level. The method can produce sintered parts whose accuracies are ± 0.004 mm/mm in the compressive direction and ± 0.002 mm/mm in the transverse direction of compression. However, from the perspective of mould clearance and productivity, as compaction uses metal powder with larger particles than MIM does, plus, unables to sinter components in a high temperature due to the distribution of the compressibility of the powder within the compacted parts, the density of sintered stainless steel components becomes relatively low like 92% or so.
MIM is a method with moderate dimensional tolerance and productivity, and compared to CM, MIM has a high degree of design freedom and higher density. The binder, is mixed with metal powder in a ratio of about 40% by volume to form components, therefore MIM has advantages over the production of complicated shapes and the mass production of relatively small components. Unlike compaction, there is no deformation of the metal powder during the moulding process, and the distribution of the metal powder in the part is uniform, therefore, deformation can be suppressed even when sintering at a relatively high temperature, thus, high density sintered parts are obtained. As MIM uses small particle size powder, feedstock development with super-fine powder possessing, high transferability is conducted. Also a possible use of the remaining powder from the AM (Additive Manufacturing) that were out of specification. Generally, HIP is often used to increase the density of sintered bodies manufactured by CM, MIM, or casted parts, but it is also used for large metal parts production from the powder. HIP powder manufacturing is only applied for a part operated in harsh environments, such as small quantities of pipe connecting parts for offshore oil drilling or very limited quantity production since the mould is single-use. When sintering using HIP, a part with high density can be obtained, however, since high-purity powder is filled in a single-use sealed container and sintered, productivity is low, and it is difficult to manufacture small parts.
Characteristics of micro-MIM technology
Micro MIM group has developed original μ-MIM technology® based on conventional MIM technology, and specialises in small and complex shaped components. With stainless steel material we can achieve more than 98.5% density, and tolerance of ±0.010 mm for components smaller than 5mm.We have pursued a method to minimise secondary process such as machining and mould design that allows us to manufacture net shape together with stable high quality. We would be glad to show you our μ-MIM components with loupe when we meet you in person.
Greetings from Düsseldorf, Germany
Hi, I am Yumi Peinemann, Marketing and Account Manager. I have been with the company since shortly before the company was founded. As the company culture encourages me to take on new challenges, I always try to come up with new ideas and work on new things every day.
In Germany, board games are very popular across all generations, and this environment made me become a board gamer. I collect board games on my travels and enjoy playing them in parks and at home. If you are ever in Germany, please stop by and let’s play German board games together!
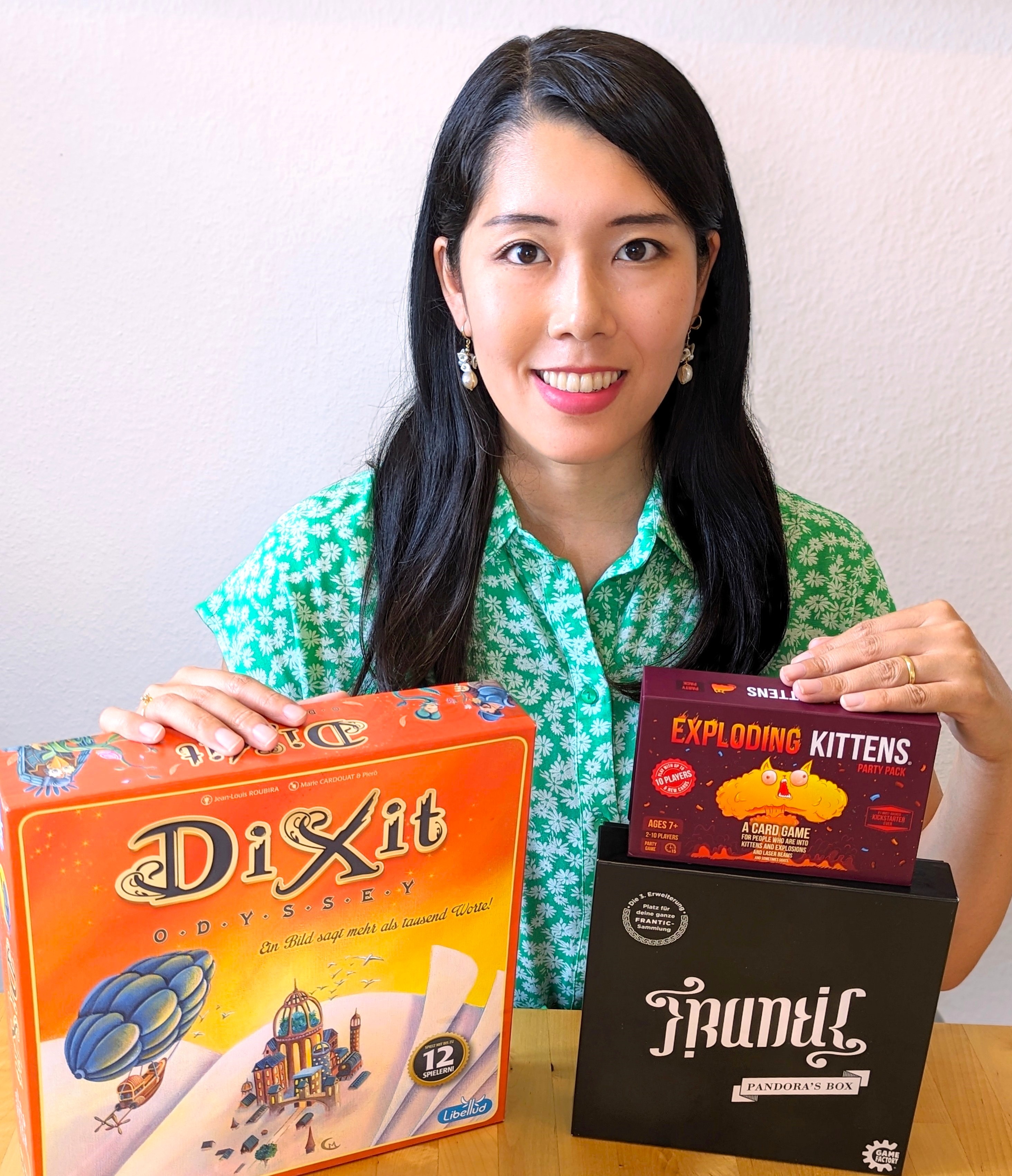
Download the PDF file
Conclusion
Cracking, slumping or blistering is commonly observed due to the binder swelling and/or residual stress difference between the surface and interior. It is possible to avoid these problems by selecting appropriate organic solvents and temperature control.
The catalytic deboning uses sublimation of binder, thus it is possible to decompose the binder in relatively short processing time with minimizing the deformation. However, with a strong acidic atmosphere, theapplicable metal material option is limited.
In the sintering process, the necking, which is bridging the metal powders by thermal diffusion, starts at the sintering temperature. Once the necking starts, the shrinking is observed and increases the density, thus before starting the necking reaction, all the organic components should be decomposed and gas between the powders should be removed. In the sintering process, the unwanted chemical reaction, such as oxidation or carbonization, leads to mechanical property loss, therefore a precise atmosphere control with low heating rate at the beginning of the process is required. Also, when it reaches the sintering temperature, some add it vegetal can be evaporated.