μ-MIM® Technical Newsletter Vol. 40: Announcement of the establishment of Micro MIM Europe GmbH
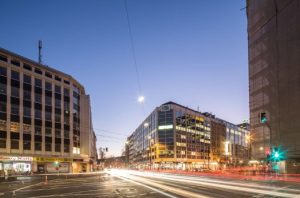
In September 2022, Micro MIM Japan Holdings Inc. established Micro MIM Europe GmbH in Düsseldorf, west of Germany. With the addition of new members, we will be able to respond more quickly to customers in Europe and North America. If you visit Germany for an exhibition or business trip, please do not hesitate to stop by.
Company name: Micro MIM Europe GmbH
Address: 406, Graf-Adolf Straße 41, Düsseldorf, 40210
Micronora
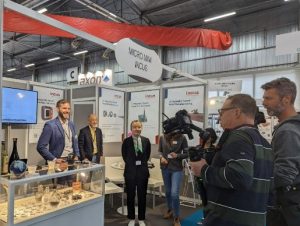
From 27th to 30th September, we exhibited at the Micronora, which is the leading microtechnology exhibition in Europe, held in Besançon, France with Incus GmbH, a manufacturer of metal 3D printers with the Lithography-based Metal Manufacturing (LMM) method. Micronora is held every two years and that was the third time for us to have a booth at the exhibition (once was virtual in 2020) and we exhibited together with our partner for the first time. Micronora 2022 was the first face-to-face exhibition after the pandemic and many visitors visited our booth from all over the world to see microtechnology components in person.
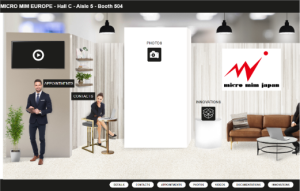
At the same time, we also had an online 2D stand as you can see the picture above, on the exhibition website for the first time. From both online and offline stands, we were able to reach more customers through the whole exhibition and to introduce our latest Micro MIM technology. We would like to express our gratitude to everyone who visited our booth and our 2D stand.
We also participated in the B2B matching meetings called Micro & Nano Event. It was a very good opportunity for many companies involved in the micro and nano industry to get to know each other and explore collaboration in the near future. We are convinced that micro-MIM technology can contribute to the development of the microtechnology industry through exchanges with companies and institutions in pioneering fields, and we look forward to further discussions and cooperation in the future.
Webinar
The webinar with a new theme of “Benefits of μ-MIM® in medical device manufacturing” will be held from November 2022 to January 2023. In this webinar we would like to show you the potential of Micro MIM technology for the medical industry, especially in regards to our AM features and to our surface treatment ability. We are looking forward to your registration to the webinar on this page!
Column
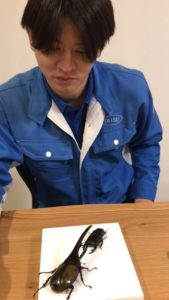
I am Seiya Morioka at the Manufacturing Department. I started working as a sales engineer as well a few years ago, which has brought me more opportunities to be involved in making prototypes. Therefore, I am able to understand the feelings and the positions of both the sales side and the mass production side. Although it might be relatively easy to make a great prototype, I always proceed with a focus on how I can incorporate this into mass production in a simple way.
My current hobby is breeding beetles and stag beetles these days and I have several species including foreign ones. I am very glad to have them of which I dreamed in my childhood. Every day I am even happier as my first child was born in July!
Conclusion
Cracking, slumping or blistering is commonly observed due to the binder swelling and/or residual stress difference between the surface and interior. It is possible to avoid these problems by selecting appropriate organic solvents and temperature control.
The catalytic deboning uses sublimation of binder, thus it is possible to decompose the binder in relatively short processing time with minimizing the deformation. However, with a strong acidic atmosphere, theapplicable metal material option is limited.
In the sintering process, the necking, which is bridging the metal powders by thermal diffusion, starts at the sintering temperature. Once the necking starts, the shrinking is observed and increases the density, thus before starting the necking reaction, all the organic components should be decomposed and gas between the powders should be removed. In the sintering process, the unwanted chemical reaction, such as oxidation or carbonization, leads to mechanical property loss, therefore a precise atmosphere control with low heating rate at the beginning of the process is required. Also, when it reaches the sintering temperature, some add it vegetal can be evaporated.